Professional Overview to Casting Aluminum : Strategies, Tips & Tricks
Professional Overview to Casting Aluminum : Strategies, Tips & Tricks
Blog Article
Aluminum Spreading Providers Introduced: Crucial Insights and Tips
Checking out the world of light weight aluminum spreading solutions can unveil a world of detailed processes and nuanced factors to consider that are essential for effective end results. As we venture into the realm of light weight aluminum casting solutions, prepare to uncover the essential components that can shape the trajectory of your projects and raise your understanding of this complex craft.
The Fundamentals of Aluminum Spreading
What fundamental processes are included in aluminum casting that develop the backbone of this commonly used production strategy? Light weight aluminum spreading is a cost-effective and versatile method used in various sectors to develop complex and elaborate metal elements. The procedure begins with the melting of light weight aluminum ingots in a heater, generally at temperatures varying from 1220 ° F to 1670 ° F, depending on the particular aluminum alloy being made use of. When molten, the light weight aluminum is poured into a pre-designed mold and mildew dental caries, where it solidifies and takes the shape of the mold.
After solidification, the mold is eliminated, and the casting undertakes ending up procedures such as heat surface, treatment, and machining covering to satisfy the called for specifications. Understanding these fundamental procedures is essential for achieving premium light weight aluminum spreadings with specific dimensions and mechanical buildings.
Different Casting Techniques Described
Discovering the numerous methods utilized in light weight aluminum spreading uses useful understandings into the diverse approaches made use of to accomplish elaborate and accurate metal components. One usual technique is sand casting, where a mold is created making use of compacted sand around a pattern of the preferred part. This method is economical and flexible, suitable for both simple and intricate shapes. An additional technique, die spreading, includes injecting molten aluminum into a steel mold under high stress. Die casting enables high accuracy and repeatability, making it perfect for mass production of little to medium-sized parts. For even more detailed styles, investment spreading is typically preferred. This method makes use of wax patterns that are dissolved, leaving a cavity for the liquified aluminum to load. Financial investment casting returns precise information and smooth coatings, making it popular in markets like aerospace and vehicle. Each casting approach has its special advantages and is chosen based upon elements such as quantity, complexity, and price factors to consider.
Aspects to Consider When Selecting a Service Provider
When choosing a light weight aluminum spreading provider, reviewing their experience and knowledge is vital for making certain quality and dependability in the production procedure. The supplier's experience in the area shows their familiarity with different casting techniques, potential challenges, and ideal techniques. It is necessary to inquire concerning the sorts of tasks they have serviced in the past, guaranteeing they line up with the complexity and specs of your very own job.
Furthermore, consider the provider's track record within the sector. Try to find evaluations, testimonials, and instance research studies that show their ability to deliver top notch light weight aluminum castings consistently. A trusted service provider will certainly usually have accreditations or associations with industry companies, showcasing their commitment to quality and adherence to market criteria.
Moreover, assess the service provider's capacities in terms of modification, volume needs, and job timelines. Guarantee that they can suit your particular demands and have the flexibility to scale production as called for. Effective communication and openness regarding expenses, lead times, and high quality control processes are also vital factors to take into consideration when selecting a light weight aluminum spreading company.
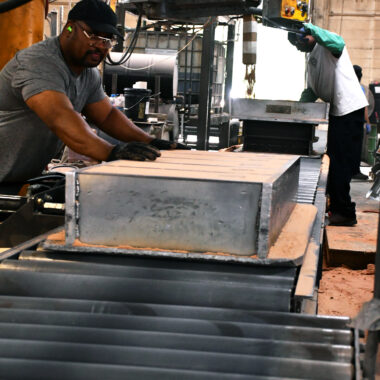
Usual Challenges and Solutions
Browsing through the complexities of aluminum spreading procedures commonly provides producers with a series of challenges that require cutting-edge options to guarantee effectiveness and high quality in production. One usual obstacle faced in light weight aluminum spreading is the development of problems such as porosity, shrinkage, or incorporations because of improper mold and mildew style or inadequate steel high quality. These defects can endanger the architectural stability of the end product. To resolve this, makers ought to carry out detailed simulations and examinations to maximize the casting procedure specifications and ensure the top quality of the molds and materials used.
One more obstacle depends on accomplishing specific dimensional precision, particularly for intricate geometries. Variations in cooling rates, mold expansion, and material buildings can lead to discrepancies discover this from the designated measurements. Executing sophisticated these details modern technologies like computer-aided layout (CAD) and computer numerical control (CNC) machining can improve precision and uniformity in light weight aluminum spreading. In addition, keeping proper control over the melting and putting procedures is vital to stop issues like overheating or uneven circulation of the molten metal - casting aluminum. By purchasing automation and real-time monitoring systems, producers can boost procedure control and decrease variants, inevitably boosting the overall top quality of aluminum actors items.
Tips for Optimizing Your Spreading Projects
By ensuring that the gating system is well-designed and appropriately placed, you can boost the flow of molten light weight aluminum and reduce the opportunities of flaws in the last casting. Furthermore, making use of computer simulations can help in forecasting and analyzing the flow of metal during the casting procedure, allowing for modifications to be made before actual manufacturing starts.
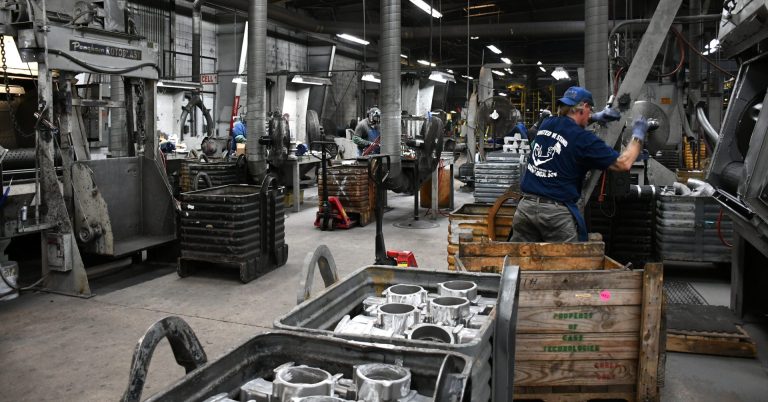
Final Thought
Finally, recognizing the fundamentals of light weight aluminum spreading, different spreading approaches, variables to think about when picking a copyright, common difficulties and remedies, and suggestions for maximizing casting jobs are necessary for successful results. By adhering to these insights and carrying out ideal services, methods and people can make sure reliable and reliable light weight aluminum spreading solutions that satisfy their details demands and demands.
Recognizing these basic procedures find more information is crucial for achieving top quality light weight aluminum spreadings with specific measurements and mechanical residential properties.
When choosing an aluminum casting service copyright, evaluating their experience and experience is crucial for guaranteeing quality and integrity in the production procedure. Efficient interaction and transparency concerning prices, lead times, and top quality control processes are likewise vital aspects to think about when choosing an aluminum spreading service provider.
Browsing with the complexities of aluminum spreading processes typically presents suppliers with a collection of difficulties that call for ingenious services to ensure performance and quality in manufacturing. One typical challenge faced in light weight aluminum casting is the development of defects such as porosity, contraction, or additions due to incorrect mold design or inadequate metal quality.
Report this page